To start thing off I have attached a couple of pictures of recent repairs I have made. Did it make sense to make these repairs? I think so.
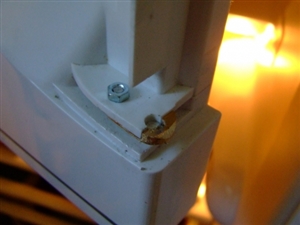
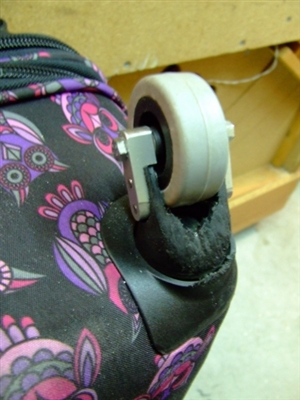
Best regards
Roger
We're about to take you to the IET registration website. Don't worry though, you'll be sent straight back to the community after completing the registration.
Continue to the IET registration site