IET Central London Evening Lecture, Savoy Place, 09-Mar-2016
Presented by Dr. Chris Sutcliffe, Renishaw AM Products Division
What exactly is 'Additive Manufacturing (AM)'? You may know it better as '3D Printing', 'Rapid Prototyping' or by a plethora of other names. That doesn't matter.
It's a "simplicity machine" that allows complexity: with it, we can make ace stuff. Such as the "Magic Arms" which help a little girl to use her arms: Body specific, pretty cheap, lightweight and quick to repair.
Chris took us on a whirlwind journey from inception to the current day, drawing on his personal experience at the forefront of this technology. (He'd just had to become an engineer at the age of 14 - the Spinning Jenny was invented on his childhood street in Liverpool.)
The samples that were passed round, and the complete mountain bike, were awe inspiring; who knew that such parts could be made in this way?
Although the machines themselves must be very complex in hardware and software, they make life very easy for the design of the end product: no custom programming is needed, just a standard CAD drawing or a scanned image (i.e. reverse engineered); it turns a 3D problem into 2D, which can then be 'printed' out in layers.
Technological and material advances are racing on - I couldn't keep up with all of the possibilities. Polymers; high-speed sintering (used on personalised footwear, we heard); Multifunctional AM to mix materials (good for laying down conductive tracks); Metals such as titanium, stainless steel and aluminium (we saw what can happen when you mix lasers with enthusiasm!); Lattice structures (can choose a design with varying geometry and density across the same part).
Presented by Dr. Chris Sutcliffe, Renishaw AM Products Division
What exactly is 'Additive Manufacturing (AM)'? You may know it better as '3D Printing', 'Rapid Prototyping' or by a plethora of other names. That doesn't matter.
It's a "simplicity machine" that allows complexity: with it, we can make ace stuff. Such as the "Magic Arms" which help a little girl to use her arms: Body specific, pretty cheap, lightweight and quick to repair.
Chris took us on a whirlwind journey from inception to the current day, drawing on his personal experience at the forefront of this technology. (He'd just had to become an engineer at the age of 14 - the Spinning Jenny was invented on his childhood street in Liverpool.)
The samples that were passed round, and the complete mountain bike, were awe inspiring; who knew that such parts could be made in this way?
Although the machines themselves must be very complex in hardware and software, they make life very easy for the design of the end product: no custom programming is needed, just a standard CAD drawing or a scanned image (i.e. reverse engineered); it turns a 3D problem into 2D, which can then be 'printed' out in layers.
Technological and material advances are racing on - I couldn't keep up with all of the possibilities. Polymers; high-speed sintering (used on personalised footwear, we heard); Multifunctional AM to mix materials (good for laying down conductive tracks); Metals such as titanium, stainless steel and aluminium (we saw what can happen when you mix lasers with enthusiasm!); Lattice structures (can choose a design with varying geometry and density across the same part).
There is a lot of hype and misconception about AM, but now we're getting onto the hype slope of enlightenment, about to enter the mainstream. Proponents need to demonstrate equivalent performance to standard manufacture and the lifetime benefits that AM can deliver. The number of parts can be reduced and weight saved (often related to reduced running costs).
This is already happening: There are tens of thousands of dental restorations per year (24 hr turn around, from a scan); 50,000 knee replacement implants per year.
To cap it all, Chris gave each of us a real-life bottle opener of titanium AM. I have had great fun, asking my friends to identify what it is, the material and how it was made.
I can't wait for AM to become truly mainstream.
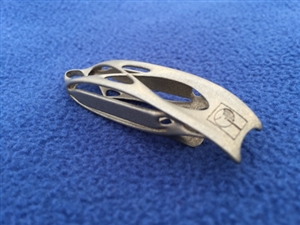