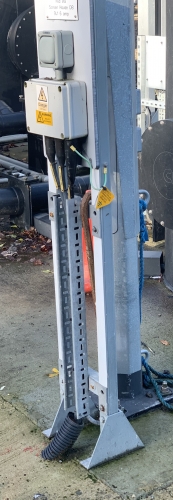
AJJewsbury:
A banjo on the outside of a plastic box probably isn't regarded as best practice either - at least if it's just trapped between the gland and the box (I can't quite see the detail in that one) - the issue is that plastic is somewhat softer than the steel of traditional enclosures, so can distort over time and result in the contact between the banjo and gland being less that tight. If you have to use a banjo with plastic enclosures the usual advise is to trap the banjo between two lock nuts inside the box so avoiding relying on the plastic to maintain a tight contact - or better still a propriatory "earthing nut" which makes a much better job of making a solid reliable contact with the thread of the gland.
- Andy.
Agreed ... these kind of products:
MrJack96:I see this a lot on sites where they’ve got an armoured cable with an earthing ring/banjo connecting the armour to an extraneous conductive part. Should there also be main bonding run as well? Common thing I see is cable tray being supplementary bonded of a local isolator usually 6mm or 10mm?
Interesting. The top of the picture is cut off, but I guess it's only got the switch and plastic box on it, nothing else?
I would have said in this case, it's possibly neither an extraneous-conductive-part, nor an exposed-conductive-part.
It certainly depends on what you term "installation" (definition in Part 2 of BS 7671 is very open to interpretation), and also whether PME conditions (and G12/4) applies, as to whether there needs to be a "main bonding run" from the entire installation MET or not.
The so reason for main bonding being such a large conductor is due to the earth resistance being taken as fairly low so high fault current?
We're about to take you to the IET registration website. Don't worry though, you'll be sent straight back to the community after completing the registration.
Continue to the IET registration site