Firstly: what checks can I best do for a possible purchase of a single ABB - AMB 630 LC16 ABA C 530kW pump unit, which is unable to be properly tested (powered up) as the plant it was operating in has been decommissioned, and is currently being scrapped.
The unit appears to be mostly self contained, with a separate 'powercap' capacitor cabinet.
There are 8 in total, in various conditions and all look like this:
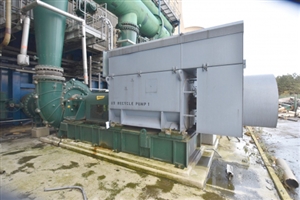
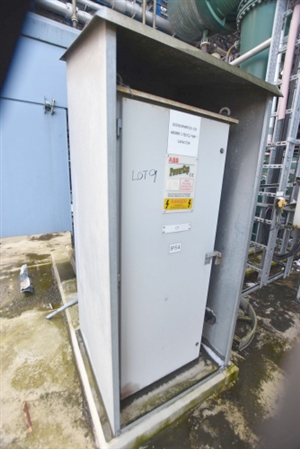
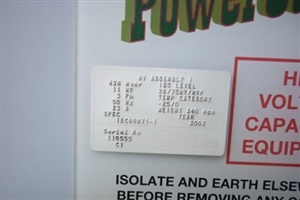
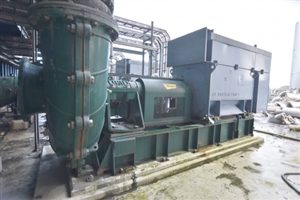
Secondly: No switching gear is 'included', however I could always ask the company (who's pulling the site apart) if it's possible to obtain the original starter systems maybe???
But would this be a good idea, considering again it's in an unknown condition.
From the 8 available, I've selected 2 that appear to be the most suitable for hopefully reusing again (not bashed about, leaking oil etc) and thus generally look ok, so possibly from that can choose the final one.... but it would be great to know how best to maybe pick the best from any testing that could be done where they stand now, without any power.
Obviously with big industrial machine as this, it's not your average consumer second-hand electrical goods....
....that one just plugs in, and then hopes it works when power is applied!
(Thanks in advance to any replies)